Resources
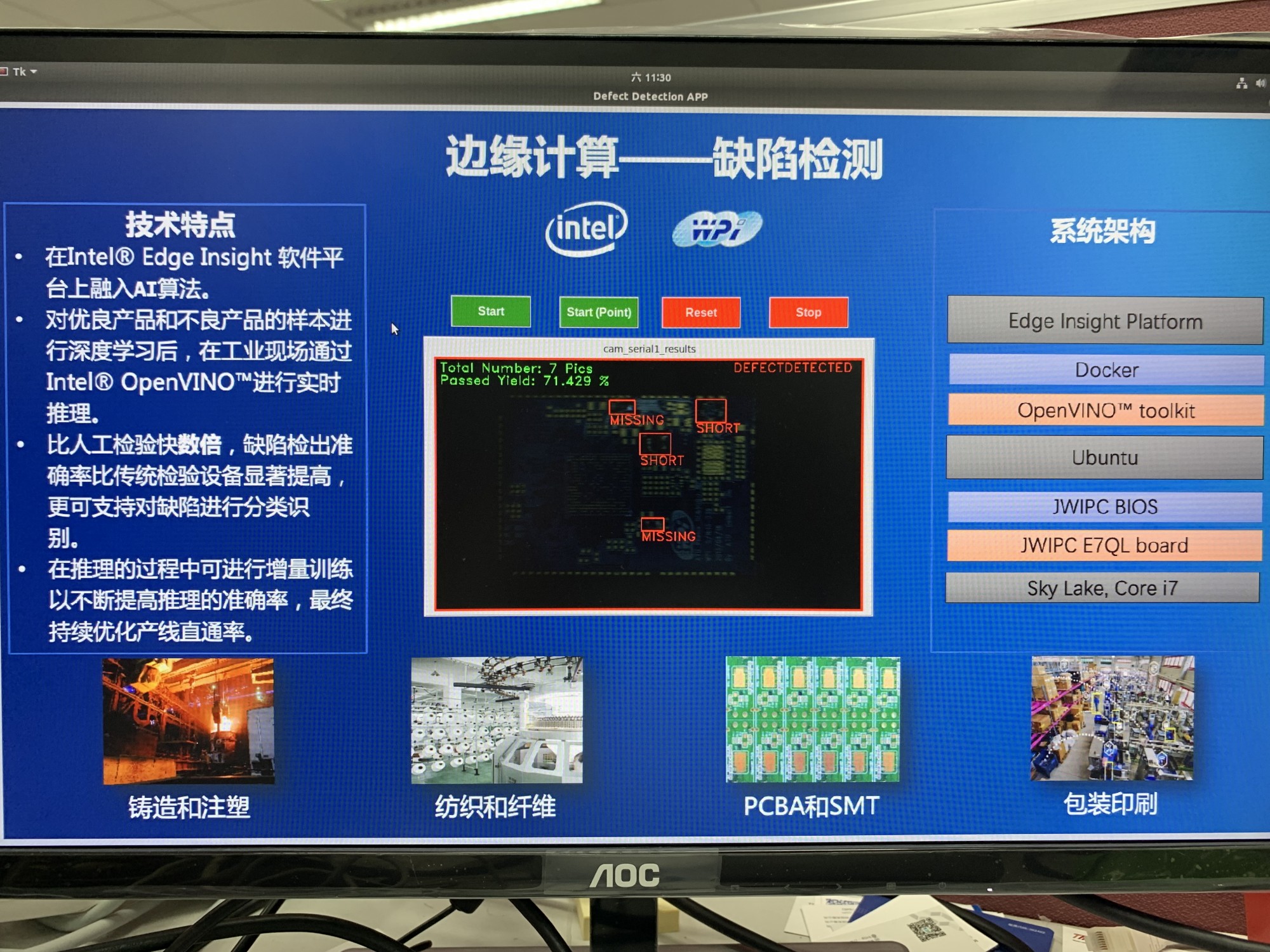
Download: Integrated Industrial Visual Inspection Scheme in Combination with Training and Inference
AIoTDescription
To meet the increasing demand for defect detection in the industrial field, Intel and WPI have jointly launched the “Training + Inference collaboratively Integrated Intel® EIS (Edge Insight Software) Industrial Visual Inspection Scheme”. The system can be used to detect the defects of products with known types by using Balser camera, gateway and software application and supporting the acquisition of high-resolution images in combination with traditional vision, deep learning and vision algorithm. The product defect detection of aluminum parts in a well-known
domestic factory is based on this framework as an example of application.
This scheme, based on computer vision, is to perform the operational processing of the acquired image data of an object through the special edge computing node device, and then to distribute the processed result:
1: Control the mechanical arm and give an alarm
2: Report the data to the edge server
The edge server collects data, processes and analyzes the data, and then completes the cloud connection.
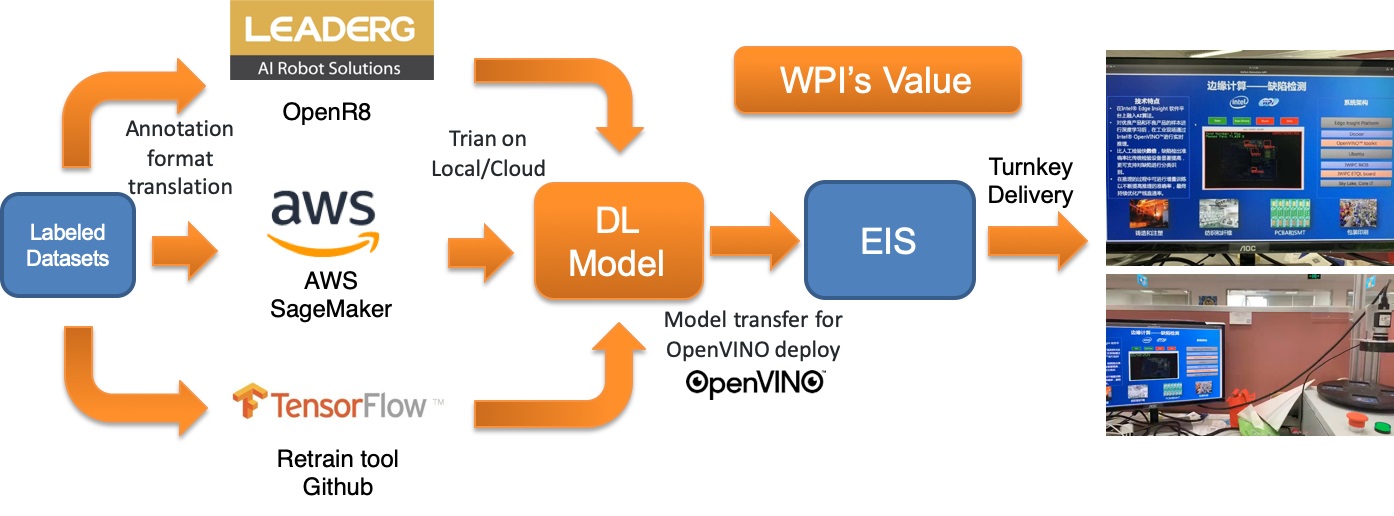
1. Advantages of the Scheme
1.1 The overfitting degree of the recognition result is low
Figure 2 Schematic Diagram of Traditional AOI Defect Recognition Scheme
Because the traditional AOI scheme adopts the optical visual comparison analysis method to analyze the object to be inspected, the inspection overfitting rate is high, it is easy to misreport good products as defective products, so manual secondary screening is required at the backstage, which affects the production efficiency and increases the labor cost. At the same time, AOI defect recognition is based on the priori defect shape to make pattern recognition, and the defect types that can be classified itself are relatively limited, it cannot judge a problem, and
then make a secondary classification.
This project bases on AI black box model for defect classification, at the same time, through the study of annotation of a large quantity of sample data, the defect target detection is automatically completed, the recognition accuracy is high, and the secondary review resources are reduced, at the same time, because the scheme uses deep learning technology, users do not need to match specific defect features, the statistics of all the features are completed automatically through artificial intelligence, so the number of defect classification can be greatly improved, compared with AOI, it can identify more subdivided defects.
1.2 Modular deployment
Usually, when an industrial project has been approved, because the application scenario varies, the system architecture often needs to be redesigned according to the project requirements, which greatly increases the complexity and difficulty of the project deployment and consumes human resources. This scheme adopts the technology of Docker modular deployment, the step function tasks including data acquisition, integration, storage, analysis, algorithm deployment, message queue processing and so on are divided, and the underlying data logic is improved, thus the replicability of the system architecture is realized, so the system Integrator does not need to redesign the scheme architecture from beginning to end, as long as the selection of functional modules, parameter setting and model re-training are completed, the deployment of the whole scheme can be basically realized, which greatly reduces the difficulty of the project deployment and improves the reusability of the system.
1.3 Low training threshold
This project adopts LeaderG's OpenR8 graphical training tool, which has built in a variety of mainstream deep learning frameworks (Tensorflow, Caffe, Pytorch...) and algorithm models (SSD, MobileNet, GoogleNet…), users can easily create a deep learning model without mastering programming skills and by simply using the mouse through a simple browser interface.
Resource Application
2.Application Cases• Greige cloth defect detection - real-time product quality inspection in the circular machine production workshop of the textile mill
• Order tracking based on image recognition - automatic order recognition of the garment factory
• Metal surface defect detection - product quality inspection of the aluminum die casting factory
3.System Configuration:
When a defective product is detected, the alarm indicator lights up. The operator shall check the product and system in detail, and press the reset button when confirming that there is no fault, the alarm indicator goes off.
3.1 Hardware scheme

Figure 4 Scheme Hardware Framework
The edge computing node of this scheme adopts the E7QL model developed by JWIPC (cooperative manufacturer) based on Intel Core Platform, which is specially designed for industrial fields. Some of its main features are as follows:
• The operating environment temperature is relatively wide, the operating temperature supports-20 to 60 degrees.
• Fanless design avoids dust.
• The chipset Q170 adopted is a specialized industrial chip with good stability.
• Different CPU from i3 to i7 is provided to meet different computing power support. The top-end core i7 has strong computing power, 4 cores and 8 threads.
• Rich industrial interfaces, supporting a series of different interfaces, such as serial port, gigabit network card, GPIO, USB3.0 and MXM3.0, etc.
• Built-in PCIE expansion slot.
• Modular design gives users different configuration choices.
3.2 Software solutions
Based on TICK time series processing architecture, this scheme realizes modular software design mode.
• Telegraf - data acquisition
• InfluxDB - data reception and storage
• Chronograf - data summary and presentation
• Kapacitor - data processing, such as monitoring strategy
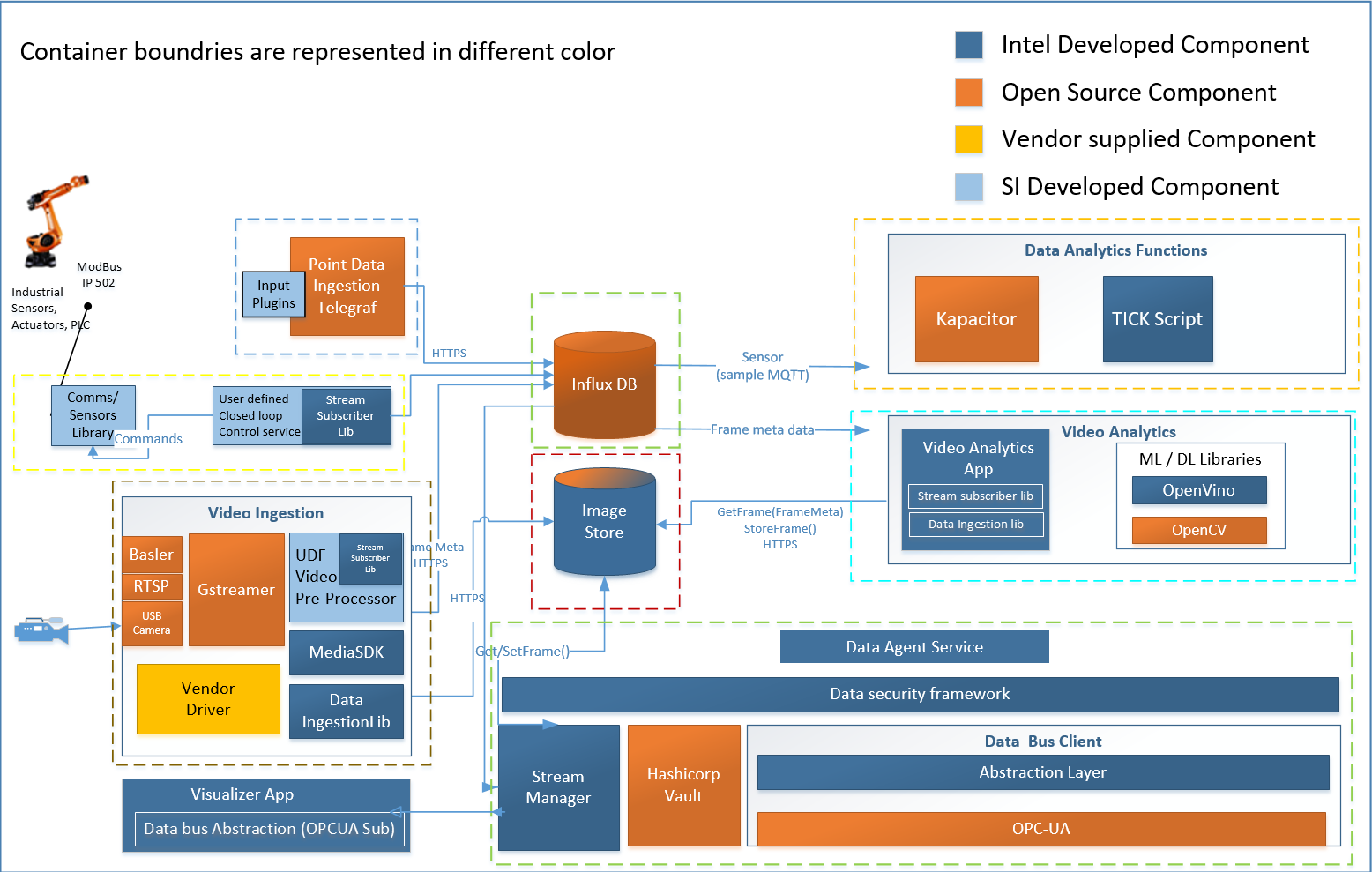
Resource Specification
4 Key Technology
4.1 Key frame screening
In this scheme, OpenCV2 built-in algorithm is adopted to collect several positive bitmaps of the object to be inspected by setting the pixel point threshold, and the frame at the center of the picture is calculated and selected as the key frame of the object to be inspected for identification. At the same time, the meta data is extracted and transferred to the InfluxDB time series database.
Figure 7 Data Acquisition Process
Figure 8 Key Frame Filtering Module Framework
4.2 Image positioning
In this scheme, OpenCV2 FlannBasedMatcher module is adopted to match the key points of the key frame with the reference picture, so as to adjust the size and angle of the key frame. Meanwhile, findHomography module is used to calculate the similarity between the reference image and the key frame and judge the validity of the key frame (whether it is the object to be inspected), so as to identify it.