Solutions
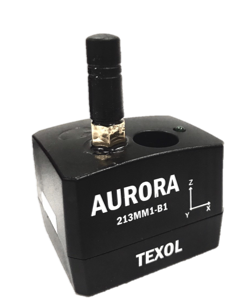
TEXOL : Smart machine monitoring system
AIoTDescription
Smart Vibration Sensor Node
The smart vibration sensor node with built-in computing and diagnostic function can collect the health condition feature of mechanical equipment in time, determine its health condition, and upload them to monitoring host through the sensor hub.
It’s applicable to all kinds of equipment with steady and continuous working equipment or non-steady equipment, such as cooling water pumps, pure water pumps, vacuum pumps, exhaust fans, or handling machinery, mechanical arm, conveyor belts etc., in factories.
The Aurora smart vibration sensor node contain vibration accelerometers, high-speed computing units, and various data transmission modules, which can execute edge-computing on high-frequency vibration signals, and only upload the vibration energy characteristics and judgment results from each component they calculated. You don't need to invest huge costs in high-efficiency spectrum analysis equipment, training of personnel spectrum interpretation, communication infrastructure deployment, and huge data storage equipment. It is the most suitable for extensive deployment of machine health monitoring framework.
The smart vibration sensor nodes of Aurora series can execute time-domain analysis, FFT spectrum analysis and conversion of vibration signals. Then calculate the overall vibration energy performance, and the vibration energy feature of various parts damage modes. You can customize the acceptable amount of energy for each damage mode. When the energy feature of a damage mode exceeds the set upper limit, Aurora will send a warning automatically. When the working speed of the equipment changes, the smart vibration sensor nodes of Aurora series will automatically search for the frequency and correspond to the order of component vibration in time. Then recalculate various energy feature to avoid the error of judgment. The analysis results are uploaded to the cloud or SCADA system through the MQTT protocol. You can know the running condition of the equipment remotely and pre-schedule the maintenance of the equipment.
The smart vibration sensor nodes of Aurora series have built-in failure models of several rotary machinery, and it can make benefit for monitoring and diagnosis on the first day of system launch. After the system is online, you can use DynaView vibration and sound signal analyzer or other tools to collect signals, and new models. Then download the new models to the smart vibration sensor nodes through Aurora data and device management software to improve the robustness of the Aurora monitoring system.
IoT Solution Application
Scenario
When you have the following diagnosis requirements, we suggest you adopt the Aurora smart vibration sensor nodes:
★ Wanting to know the health status of the field equipment and whether there are assembly or parts damage problems in real time.
★ Wanting to estimate the appropriate repair time for field equipment.
★ There are numerous machines and equipment on site, but the budget that can be invested in the monitoring system is limited.
Case Study
★ Adopt the smart vibration sensor nodes of Aurora series to monitor health condition of the reducer of the panel handling equipment.
★ Adopt the smart vibration sensor nodes of Aurora series to monitor health condition of the panel handling mechanical arm, and integrate with the panel factory FDC system for data uploading.
★ Adopt the Aurora series to monitor health condition of roll bearings in paper formation factories.
IoT Solution Specification
Model
The smart vibration sensor nodes of Aurora series adopt various types of vibration accelerometers, high-speed computing units, and data transmission modules to build various models. So that they can adapt to different deployment requirements on site.
★ 211HM1 -B1 Single-Axis Bluetooth Smart Sensor Node
★ 213MM1 -B1 Triaxial Bluetooth Smart Sensor Node